Research
Our research lab has received funding and materials from the following sources:
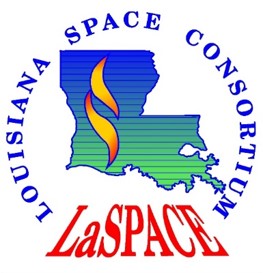
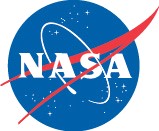
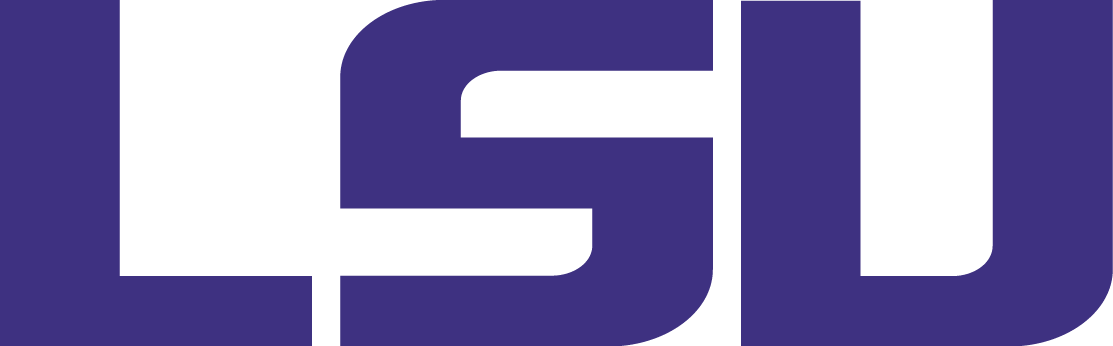
Advanced Manufacturing for Polymer Composite Materials
Funding: NSF CAREER, LA Board of Regents Research Competitiveness Subprogram
Thermoplastic polymers soften and may be formed again when heated up above a certain temperature. This makes thermoplastic composites (TPCs) more sustainable than conventional thermoset composites as they can be reused and recycled. An additional benefit is that they may be joined through fusion bonding, otherwise known as "welding", eliminating the use of mechanical fasteners, thus reducing weight, CO2 emissions and costs. However, in order for welded composite joints to be considered in industrial applications, especially for high-performance sectors such as aerospace, it is imperative to increase confidence in their structural integrity and fundamental prediction of failure behavior. The main goal of this project is to enable structural health monitoring (SHM) and repair of ultrasonically welded thermoplastic composite joints. This will be achieved through multifunctional nanocomposite thin films placed at the welded interface. These films will fulfill three purposes: i) Energy directors for the welding process, ii) Strain sensors for structural integrity monitoring, and iii) Heating elements for directed repair.
Brief demonstration of welding process with nanocomposite energy directors (unidirectional GF/PP adherends).
Funding: NSF CAREER, LSU Graduate School Economic Development Assistantship
The overall goal of this project is to enable multiscale manufacturing methods for thermoplastic-matrix composites through high-power ultrasonics. Ultrasonic consolidation occurs under the application of pressure and heat generation through frictional and viscoelastic heating. The polymer matrix melts and infuse dry fibers to fill micro- and macro-voids in a matter of milliseconds. The advantage of this method is its high speed and lower cost compared to traditional techniques such as compression molding, but novel in-situ experimental approaches must be develop to understand the physics behind the process. Ongoing work includes: 1) temperature profile measurements during consolidation to determine crystallization kinetics, 2) real-time flow visualization through an optical welding frame, and 3) multiscale properties improvement of additively manufactured geometries under ultrasonic consolidation.
Funding: LaSPACE NASA EPSCoR RAP and REA Programs + Boeing and Solvay for aerospace-grade prepregs
Carbon fiber (CF)/epoxy has become a common material in multiple industries, especially aerospace. Fabrication of large and complex structures is possible, but throughout their service life, they may experience severe loading conditions and become damaged. While replacing the damaged component is a solution, repair is a more cost-effective approach. One effective method is bonded overlap or scarf repair, but requires several steps to complete: removal of damaged plies, scarf of the parent structure, surface preparation, adhesive application and patch consolidation. The latter is usually carried out by vacuum bagging, followed by curing with an autoclave, oven or heated blanket. This process is time-consuming and can be costly.
Therefore, this project explores the feasibility of a cost- and time-effective repair technique for CF/epoxy composites using ultrasonic vibrations and flat repair patches. It is expected that ultrasonic vibrations application prepreg layers will increase temperature in the thermoset polymer through frictional and viscoelastic heating, promoting resin flow, compaction, and potentially, polymerization. Using ultrasonic welding, vacuum bagging would no longer be necessary for repairs, reducing manufacturing time by at least 40%. In order to assess the feasibility of this process, the effect of welding parameters (i.e. pressure, duration, amplitude) is studied on temperature generation, void content (Figure 1a) and mechanical performance of laminates. Short-beam shear and open-hole tests (Figure 1b) indicated the ultrasonic process led to similar manufacturing quality and mechanical performance as vacuum bagged reference samples.
(a)
(b)
Figure 1. (a) Experimentally-measured temperature profile through the thickness during application of ultrasonic vibrations on 12 plies of UD CF/epoxy prepregs - left axis is the sample thickness in mm and right axis is the temperature in oC (25% travel, 100 N force and 38.1 microns amplitude), and (b) Strength recovery of repaired open-hole specimens with vacuum bagging (VBO) and ultrasonic welding (USW). (Reference: D. Hoskins and G. Palardy, "An investigation of high-speed consolidation of carbon fiber - epoxy composites through ultrasonic welding", The Composites and Advanced Materials Expo, CAMX, Anaheim, CA, September 23-26 2019).
Funding: LAMDA Seed Funding Track1B: Collaborative Partnership Award
More coming soon.
Material Behavior and Characterization
Funding: LSU Board of Supervisors (LIFT2)
Coming soon.
Coatings for Meshes and Composites
Funding: LSU
The aim of this project is to create flexible composite fabrics and structures combining multi-material constituents. An example of application is implants for emergency use, where custom-made or 3D printed geometries might not be readily available. For instance, coating metal or polymer substrates with biocompatible nanoparticle thin films can lead to improved mechanical properties with good flexibility. Sol-gels of hydroxyapatite (HA) or HA-based nanocomposites, metal fabrics and 3D printed polymer fabrics are investigated and characterized for microstructure, hardness, tensile properties, corrosion and biocompatibility.
Augmented Reality as a Training Tool
Funding: NSF CAREER / LSU
Project outcomes from Capstone Design Team 59 (2022 - 2023): Christopher Vasquez (ECE), Anthony Stovall (EE), and Katie Gonsoulin (ECE).
(a)
(b)
Figure 2. (a) The training tool includes an Augmented Reality (AR) headset (Hololens 2) and a lighting system. A user is shown wearing the headset while interacting with the AR interface (seen on the laptop screen). (b) Actual user interface as seen through the AR headset. It features movable holograms with detailed instructions, images, videos, expandable 3D models, materials data sheets, and educational information. The lighting system is used to indicate tools location and timer duration, and to provide interaction during educational questions. Photo credit: Capstone Team 59 (2021-2022).