Existing Projects
Nanolayer grain boundary complexions and solid-state activated sintering in refractory
metals/alloys
This research leverages processing-microstructure-property relationship in bulk nanocrystalline refractory metal alloy powders to improve the manufacturability of high-temperature components. The goal of this project is to control tansformations of thin nanolayer grain boundary complexions (i.e., amorphous interfacial films) and trigger solid-state activated sintering mechanisms to reduce necessary sintering temperatures, applied pressures, and time.
Sintering pure refractory powders is difficult because high processing temperatures (e.g., ~1800 °C) are required to trigger atomic diffusion. One strategy to improve sinterability of refractory powders is to incorporate transition metals that 'activate' densification. This research utilizes the synthesis of base refractory metals like molybdenum and tungsten with intentionally added transition-metal activating species, like chromium and nickle through cryogenic high energy ball milling. This project applies thermodynamic principles to predict alloy compositions, taking into account the presence of unintentional yet practical non-metal impurities such as carbon, nitrogen, and oxygen. Pressureless and pressure-assisted sintering will be conducted to assess the effectiveness of the alloy design principles and predictive tools. The grain growth kinetics and grain boundary complexion transformation/percolation will be studied using atomic-scale characterization tools.
This research also aims to link the sinterability of powders, activated by complexions, to their production method - whether using laboratory-scale or industrial-scale cryogenic ball milling - to evaluate their potential for large-scale manufacturing of bulk nanostructured refractory powders.
Friction Stir Additive Manufacturing (FSAM) is an innovative large-scale thermomechanical additive manufacturing process. In FSAM, metallic feedstock bars are plastically sheared and deposited layer by layer onto a substrate. The shear forces generated during the process create frictional heating, which softens the feedstock and enables seamless layer deposition.
However, given the need of significant plastic deformation, FSAM has mostly been limited to relatively soft aluminum-based or copper-based alloys. Therefore, components requiring high strength for demanding applications are not as easily obtainable using FSAM. A key strategy for depositing high-strength materials involves producing stronger feedstock rods from powder green bodies (compacted but unsintered powder forms), a process referred to as Friction Stir Powder Additive Manufacturing (FSPAM). The objective is to create feedstock rods by hot extruding powders into consolidated rods with the same dimensions as existing solid feedstock rods. The main challenge of using powder feedstocks lies in the added complexity of optimizing various input processing conditions - such as particle size distribution, purity, and morphology - to consistently produce high-quality parts. This project is based on optimising new alloy compositions to scale-up FSPAM.
Complex Concentrated Alloys (CCAs) such as NiCoCr and NiCoCu have been identified because of their advantageous phase transformation properties. The research focuses on synthesizing these powder compositions followed by microstructural characterization using microscopy and evaluating mechanical properties. The goal of this project is to systematically explore processing parameters such as milling temperature, milling time, ball to powder ratio, and additions of process control agents to fulfill the need to generate feedstock rods supporting FSPAM.
WC-CoCr cermet coatings possess superior wear and corrosion resistant properties. High Velocity Oxy Fuel (HVOF) technology is known for producing cermet coatings with high density and low porosity. However, this method is costly and may not be practical for application as internal pipeline coatings.
In this research, the Atomospheric Plasma Spraying (APS) technique is used to produce dense WC-CoCr cermet coatings with physical and mechanical properties comparable to those typically achieved with HVOF. APS is chosen for its cost-effectiveness, ease of use, industrial scalability, and suitability for internal linings.
The goal of this project is to understand the relationship between various processing conditions in the APS system and the resulting microsctructure of the coatings, with the ultimate aim of achieving the desired mechanical and physical properties. This provides an opportunity to study the microstructure and gain insights to the core phenomena. These findings can then be correlated with processing conditions to enhance coating quality, with the ulimate goal of replacing the complex HVOF process with the simpler APS.
Nitride coatings are among the most effective solutions for preventing hydrogen permeation into substrate materials. However, current technologies like physical vapor deposition (PVD) produce these coatings as thin films, limiting their application to laboratory-scale experiments and making them unsuitable for large-scale industrial production. This project seeks to overcome these limitations by leveraging the reactive environment capabilities of the Atmospheric Plasma Spray (APS) system to develop nitride based composite coatings. These coatings aim to reduce hydrogen ingress and mitigate hydrogen-induced degradation phenomena, such as hydrogen embrittlement and hydrogen-assisted cracking.
The use of composites is necessary because nitrides, while highly reactive, cannot be effectively used alone to form coatings with APS. We exploit the reactive nature of the APS system, using nitrogen as the primary gas to create a reactive environment for producing TiO₂-TiN and Al₂O₃-AlN composite coatings.
For TiO₂-TiN coatings, TiN is used as the initial powder, with process variables optimized to control the conversion to TO₂ and adjust the composition distribution in the microstructure. For Al₂O₃-AlN coatings, Al₂O₃ is used as the initial powder, with process parameters refined to enhance the conversion to AIN and achieve dense coatings.
We use experiments, advanced characterization techniques, evaluation of mechanical properties, and the study of hydrogen permeation behavior to improve the performance and applicability of these coatings.
Electronic Microscopy Sight (“EMSight”) is an Augmented and Virtual Reality (AR/VR) technological approach used to rapidly train a wide range of current and emerging agency, industry, and university users in advanced microscopy, materials analysis, and characterization techniques.
Materials and manufacturing science is now an economic, energy, and national security issue, and while tools and technology have developed, the technical talent needed to use these assets has not. Louisiana State University (LSU) has been awarded by NASA for developing a fully operational Digital Twin of NASA’s New Orleans Michoud Assembly Facility (MAF), a 2,000,000 square foot manufacturing facility responsible for building and assembling the rockets and Orion crew capsules for Artemis - the U.S.’ next manned space missions.
EMSight uses LSU's proven Digital Twin capabilities from its previous project with NASA, and integrates it with its expertise in electron microscopy to create an interactive mixed-reality application. This tool accelerates material design and development while offering valuable insights into material performance across various use-inspired applications.
The goal of this project is to develop EMSight as a tool to enhance the effectiveness of microscopists by streamlining decision-making and analysis. EMSight enables users and collaborators to visualize contaminants, explore materials at the atomic scale, and compare current data with prior experimental results. This capability allows for rapid identification of microstructural issues, saving months of effort and revolutionizing workflows. By advancing materials development and analysis, EMSight addresses critical needs in industry and defense, particularly in the context of the growing trend towar reshoring fabrication and manufacturing.
Oxides with fast ion-conduction are crucial components for a wide range of applications including batteries and solid-oxide fuel cells, which are needed for societal adoption of renewable energy technologies. However, progress in the research and development of ion-conducting ceramics has been sluggish, as time-consuming synthesis and sintering act as a bottleneck to new materials discovery. The project team will leverage their ultra-high-temperature synthesis technique that can rapidly sinter oxide materials in about 10 seconds, integrated with computational modeling and high-throughput measurements, to accelerate the discovery and design of novel oxide materials. The integrated closed-loop framework will advance a general paradigm for materials design and discovery in a fraction of the time of conventional discovery. Through this project, novel sodium-ion conducting materials will be discovered, which can be used for sodium batteries as economic, environmental-friendly, and sustainable alternatives to lithium-ion batteries for renewable energy storage. In addition, this project will leverage the interdisciplinary research program to create unique educational opportunities for a diverse group of graduate, undergraduate, K-12 students, and under-represented minorities.
New Projects
Reactive materials are thermodynamically metastable and undergo highly exothermic reactions upon applied stress or heat. The reactive materials community made great progress in correlating ignition and combustion of reactive materials to bulk granular features (e.g., particle size dstribution, particle morphology, grain size, void topology, etc.). However, mechanisms related to atomic-scale internal interfaces, such as internal heterophase boundaries, were relatively unexplored.
The solid-state interfaces community put forth a new paradigm of 'interfacial engineering’ that utilizes the phase-like behavior of interfaces to control bulk material properties such as atomic diffusion and thermal conductivity. The latest developments of 'interfacial engineering’ have not been applied to reactive materials. The overarching goal of this hypothesis-driven research is to integrate these fields of study. The specific objectives are to identify atomic mechanisms linked to subgranular features affecting reactivity, use interfactial transformations to optimize ignition and combustion in nanostructured reactive materials, and employ advanced atomic-resolution electron microscopy to observe interfactial reactions and deepen the understanding of microstructure-controlled reactive materials.
Aluminum-based thermite will be studied as a model system to develop a theoretical/computational toolbox that predicts interfacial transformations, investigate how high energy powder processing and low-temperature annealing treatments modify interfacial structures using advanced characterization techniques, and perform thermoanalytical measurements and ignition burn rate experiments to correlate interfacial phenomena to energetic properties.
This research aims to fundamentally understand interfacial diffusion in ceramics by studing rare-earth elements such as Europium, doped in parts-per-million quantities into magnesium aluminate spinel (MgAl₂O₄), which serves as a model system. The focus is on correlating changes in grain boundary structure, thickness, and composition (referred to as complexion transitions) with variations in interfacial diffusivity. This is achieved through high-throughput characterization combined with simulations and calculations to elucidate atomic mechanisms.
A key aspect of the research involves observing complexion transitions and utilizing atomic-resolution electron microscopy to decouple the segregation factor from grain boundary width during quantitative analysis. Unlike prior studies that primarily link diffusivity changes to misorientation (e.g., high-angle grain boundaries) or coincident site lattice (CSL) boundaries, this work uses a diffusion couple approach. This approach provides controlled dopant concentration gradients, confining thermodynamic and kinetic conditions of complexion transformations to enable precise studies of these transitions and their effects on diffusion.
This project employs a comprehensive methodology that includes doping, sintering, and post-sintering high-temperature heat treatments experiments. Advanced characterization techniques, such as microscopy, diffraction, and spectroscopy, are combined with Monte Carlo simulations and Density Functional Theory (DFT) calculations. The ultimate goal is to generate universal knowledge that can guide the design of next-generation materials with enhanced performance.
Professors Anthony Engler, Phillip Sprunger, Revati Kumar, and Christopher Marvel of Louisiana State University (LSU) will design, synthesize, and investigate new polymeric materials and processes for high-resolution patterning in semiconductor manufacturing. Experiments at the LSU Center for Advanced Microstructures and Devices (CAMD) synchrotron will enable industrial and academic researchers in the Southern U.S. to access high energy photons used in state-of-the-art manufacturing systems. This project will develop new classes of EUV-sensitive polymers, investigate their fundamental interactions with photons and electrons, and co-design the materials with metrology and pattern transfer processes. This award will also help launch a Semiconductor Fabrication Workshop that will teach the semiconductor manufacturing process and provide hands-on training in cleanrooms to students.
This project is specifically focused on the design and synthesis of new polymers that can serve as dry-developed, chain scission resists for EUV lithography and the construction of an EUV exposure module. Chain scission resists (CSRs) have the potential to improve line edge roughness and resolution limit due to a lack of photoactive small molecules that can diffuse to reduce patterning fidelity. This research will design new classes of polyaldehydes that are inherently sensitive toward EUV photons, or the secondary electrons produced during exposure, and harness their relatively low thermodynamic ceiling temperature to achieve chemical amplification via depolymerization during the post-exposure bake. These materials will be co-designed with critical, downstream processes of photoresists, including metrology and pattern transfer needed to reliably fabricate advanced devices. The research will utilize custom operando EUV experiments, state-of-the-art electron microscopy, and molecular dynamics simulations to provide fundamental insights into polymer interactions and mechanisms during EUV exposure and development. This polyaldehyde platform will enable next-generation semiconductor fabrication processes with their low energy transformation from solid to vapor.
Current & Past Funding Support
Industrial Collaborations
Academic Collaborations
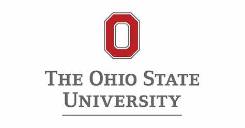
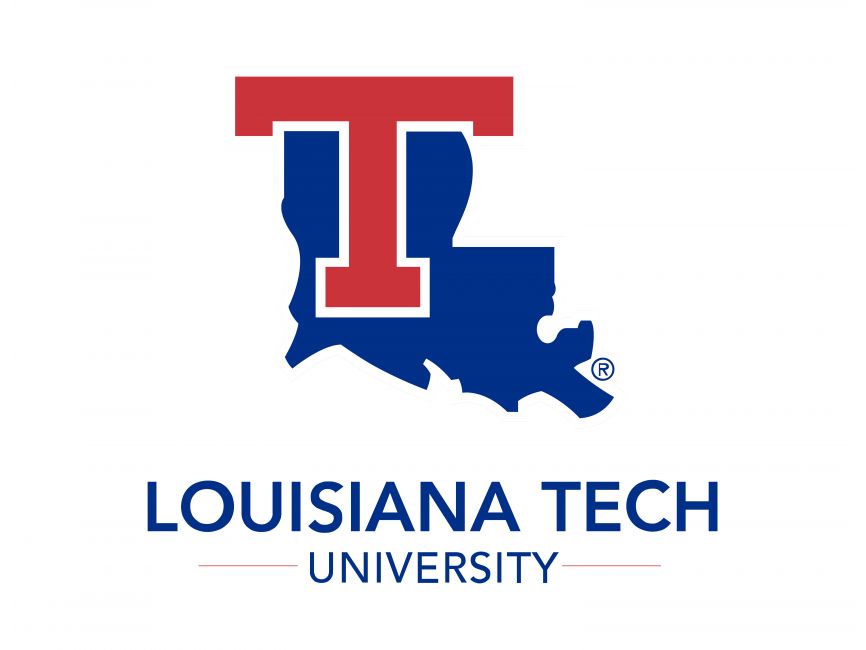